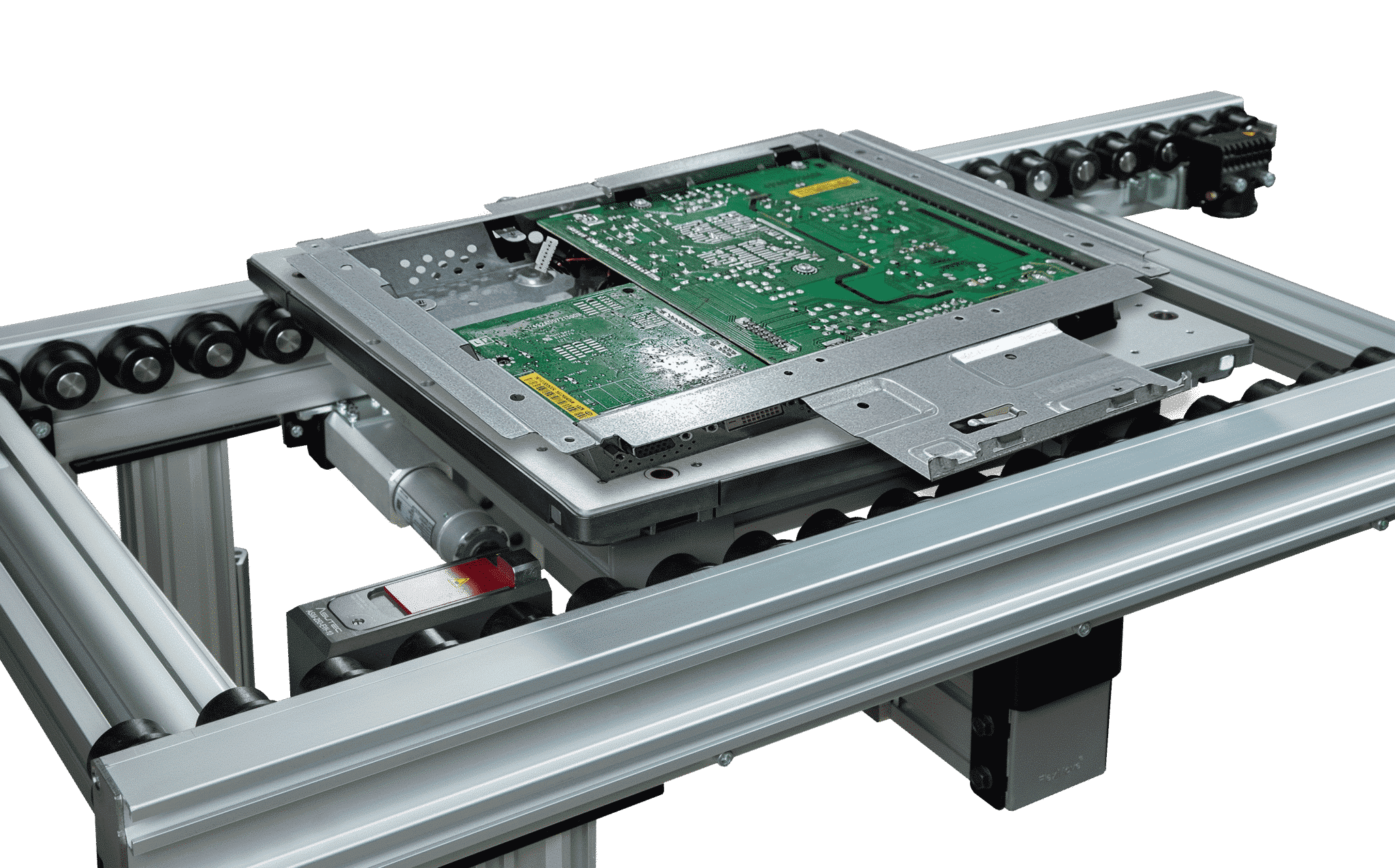
In the highly competitive realm of computer monitor manufacturing, Dorner’s state-of-the-art conveyor systems prove instrumental in optimizing production processes, adding efficiency, and improving product quality in assembly operations. This application study offers a detailed exploration of how Dorner’s line of pallet system conveyors serves manufacturers across multiple stages in computer monitor production.
Sub-Assembly
The monitor manufacturing journey begins in sub-assembly with the production of display panels, circuit board assembly and wiring, and the casing and stand preparation. While these parts will all go into the final product, their handling and assembly requirements vary greatly. From delicate circuit boards and LED arrays to plastic injection molding and mechanical parts production, Dorner offers pallet system conveyors to meet the unique needs of each process.
Circuit Board Assembly
The circuit board assembly is the most delicate component in computer monitor manufacturing. Dorner’s ERT150 conveyor is ideal for this critical step. The ERT150, equipped with non-static sensitive ESD rollers, ensures the safe movement of circuit boards, while its cleanroom verification aligns seamlessly with the precision required when handling electronic components. Because of the delicate nature of circuit board production, the ERT150 was also beneficial because of the no back pressure accumulation system which provided product safety.
Other Benefits of ERT150 in Circuit Board Production:
- Easily Reconfigurable
- Robotic Integration
- Automated Monitoring
- Safe Human Operator Interfacing
Display Panel Assembly
For the larger monitor displays that are increasingly in demand, the ERT250 provides a larger pallet surface than the ERT150, while still offering the same static dissipative and gentle product handling features. Like the ERT150, the ERT250 is an easy-to-integrate system with a variety of lifting and transfer modules to ensure accurate product interfacing with robotics and automation technology. This makes it an ideal solution for highly complex display panel assembly applications.
Plastic Housing & Injection Molded Parts
Advancing the injection molding plastic process, Dorner partners with another CMCO Conveyance Group brand, montratec, with their innovative montrac® system. This system operates on a sophisticated monorail, providing a high degree of flexibility and adaptability for the intricate demands of the injection molding process. The montrac® system excels in efficiently transporting materials through the molding stages, contributing to a seamless casing production process. The montrac® system offers a number of process advantages such as speed, flexibility, and modular design.
- Speed: Moving products at high speeds is the goal of every manufacturing operation but doing it precisely and safely is another story. The montrac® system utilizes controls and safe pallet locks to push products at unmatched speed to continue product and improve throughput.
- Flexibility: Utilizing a monorail shuttle system can be beneficial for operations that require versatility to accommodate footprint and elevation change requirements.
- Modular Design: The modular montrac® components adapt to a wide range of product sizes and production volumes. Pre-configured and pre-tested modules ensure fast system installation and minimize downtime, and the independence of the modules allows for easy reconfiguration and expansion.
Main Assembly
In pursuit of producing hundreds of monitors daily, monitor manufacturers turn to Dorner’s cutting-edge DualMove Pallet System for their main product assembly operations. The conveyor system is equipped with T10 timing belts, ensuring precise and secure transportation of pallets to individual touchpoint stations.
At each assembly station, Dorner’s DualMove offers versatility with three essential accessory modules:
Lift & Transfer: Safely and efficiently lifts pallets, precisely placing them on the correct assembly line, contributing to a streamlined workflow.
Lift & Rotate: Facilitates orientation adjustments, crucial when human interaction is required at specific assembly points, optimizing the ergonomic aspects of the assembly process.
Lift & Locate: This module plays a pivotal role in the inspection phase, ensuring the precise location of products for thorough quality checks.
Packaging
Finally, after assembly and testing is complete, monitors continue DualMove conveyors for packaging. The DualMove was the right solution for this packaging solution because of the easy integration into the rest of the line and was able to withstand the weight due to a higher weight rating and was able to be sized properly to fit grouped packages that were being prepped for palletization.
Utilizing a complete line of Dorner & montratec products company was able to curate an ideal solution that provided speed, product security, and the ability to maneuver around their footprint in the most efficient way. This highlights the versatility and the wholeness of Dorner’s pallet system line which allows a company to meet their needs in a single source.
If you are looking for more information on how Dorner’s pallets systems, please contact us or visit our webpage, www.dornerconveyors.com/products/pallet-systems.